The annealing temperature is one important heat treatment parameter. What are the other important parameters for annealing of copper, steel, aluminum and similar materials? The article will discuss them all.
- The basic process: The material is heated to such a temperature where it almost starts glowing followed by a slow cooling. For the different types of steel, the elevated temperature is little higher than austenic temperature. See the picture below:
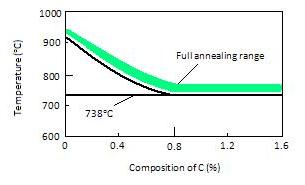
Image source: wiki
- Temperature: The temperature at which the material in question to be elevated varies not only from material to material but also from alloy to alloy of same material. For example, from the above picture (Fig.1) you can see that the annealing temperature (the green zone) varies with the percentage of carbon in case of steel. The below list will help you getting an idea about the elevated temperatures required for different materials:
Steel grade 304 – 1010 to 1120 Degree C
Steel grade 316 – 1010 to 1120 Degree C
Steel grade 309 – 1050 to 1150 Degree C
Steel grade 310 – 1050 to 1150 Degree C
Steel grade 321 – 1050 to 1150 Degree C
Steel grade 3Cr12 – 700 to 750 Degree C
Steel grade 430 – 750 to 760 Degree C
Copper alloys – 1400 to 1750 Degree C
Phosphor Bronze – 900 to 1250 Degree C
Nickel silver – 1100 to 1500 Degree C
Glass – 475 to 515 Degree C
Aluminum alloy(2017) – 335 to 350 Degree C
- Cooling rate: Slow cooling is what is desired for getting good results. But how slow? The following list will give you an idea:
Steels – should take around 1 day to cool Copper alloys – should take few hours to cool Aluminum alloy (2017) – cooling rate is around 28 Degree C per hour
- Types: Many classifications are used across the industry. Two important categories among them are: process and Full annealing.
- The first one is the softening the material in between some forming process (like cold rolling). The aim here is to remove the hardness generated due to the forming process so that while performing the further cold working operation the material should not break.
- The second one is performed before starting the cold working process itself to make the material soft enough to shape in a cold working process.
Related Book References:
Hi, I am Shibashis, a blogger by passion and an engineer by profession. I have written most of the articles for mechGuru.com. For more than a decades i am closely associated with the engineering design/manufacturing simulation technologies. I am a self taught code hobbyist, presently in love with Python (Open CV / ML / Data Science /AWS -3000+ lines, 400+ hrs. )